低サイクル疲労の特徴
大型構造物の部材などが降伏点を超える大きな応力あるいはひずみの繰返し荷重を受けて疲労破壊することがあります。構造物が受けるこのような過大荷重によって10の4乗から10の5乗程度のサイクルオーダー以下の繰返し数で破断するような大きな応力振幅条件下では、応力に対するひずみ成分に塑性ひずみ成分が含まれており、この寿命領域での疲労破壊現象を低サイクル疲労と呼びます。
また、高温機器においては機器の起動・停止に伴って部材に発生する熱応力が材料の降伏点を超えることがあり、この場合の疲労現象も低サイクル疲労となります。この高温疲労ではひずみの大きさだけではなくて時間因子も疲労寿命を支配する重要な要因となります。これは、高温下での変形がクリープ変形を伴う時間依存型の現象であること、さらに酸化の影響も高温では大きくて無視できないためであります。ここでは、高温クリープを伴った低サイクル疲労については触れないことにします。
図1に、低サイクル疲労のS-N曲線のイメージ図(鉄鋼の場合)を示します。低サイクル疲労のS-N曲線は通常、ひずみの大きさと破断までの繰返し数の関係で両対数表示されます。ひずみ成分に塑性ひずみ成分が加わる実線部分が低サイクル疲労の主要部分の線図で、10の4乗から10の5乗の繰返し数以下の範囲で疲労破壊します。
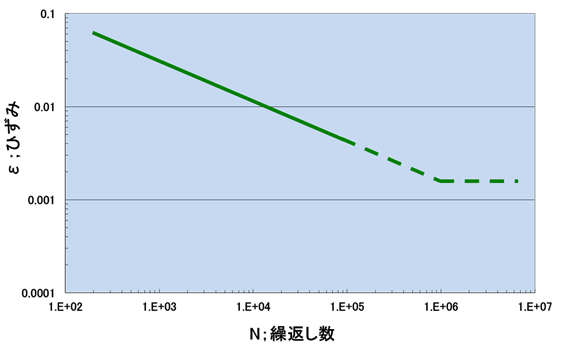
図1 低サイクル疲労のS-N曲線のイメージ図(鉄鋼の場合)
ここで、塑性ひずみを伴う大きな応力振幅条件で疲労試験を行う場合を考えてみます。応力一定の負荷条件で試験を行いますと試験体の一方向に塑性ひずみが蓄積していって大きな塑性変形が起こってしまうことがあります。そのため、一般的に低サイクル領域の疲労試験では両振りのひずみ制御の条件下で疲労試験が行われます。
試験体が両振りの塑性ひずみ成分を含む繰返しひずみを受けると、ひずみに対応する応力がわずかに減少する場合と増加する場合があり、応力-ひずみ曲線は繰返し数ごとに変化します。図2に、塑性ひずみ制御試験下の繰返し応力-ひずみ応答の例を示します。ひずみの繰返しによって応力が減少する図2 (a)は繰返し軟化、応力が増加する図2 (b)は繰返し硬化とよび、図2 (a)の繰返し軟化材には冷間加工材や熱処理硬化材が該当し、図2 (b)の繰返し硬化材には焼なまし材が該当します。前者の加工硬化により強化された材料や調質鋼などは転位の再配列によって繰返し軟化の挙動を示し、後者の焼なまし材料では転位の増加によって繰返し硬化の挙動を示すと考えられています。両者ともある程度の繰返し数の後は、軟化・硬化の現象は飽和して一定の応力-ひずみ曲線を示すようになります(図2 (c))。
機械構造物などで発生する低サイクル疲労はひずみ制御状態にあると考えるのが妥当とされており、機械構造物の該当部位を模した試験体に対して、ひずみ制御低サイクル疲労試験を行うことで寿命予測することになります。実用上の機械構造用鋼材では繰返し軟化および硬化が必ずしも定常状態に達することなく、部材の最終破断まで進行してしまうケースもあります。
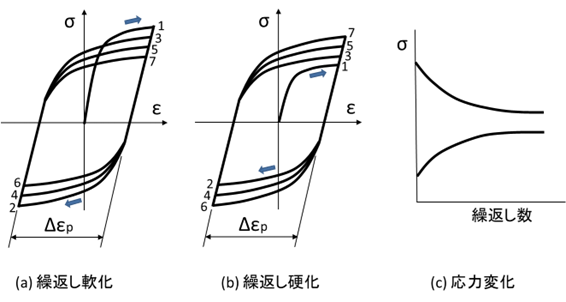
図2 塑性ひずみ制御試験下の繰返し応力-ひずみ応答の例
次に、疲労破壊した破面ではビーチマークと呼ばれるマクロ的な縞状模様が観察されることがあります。ビーチマークは繰返し荷重の大きさが時間に対して変化する場合に発生し、一定の繰返し荷重が破断まで連続して繰返されるケースでは発生しません。ビーチマークが発生しやすい応力負荷のケースとして機器の起動・停止といった繰返し稼働が考えられます。図3に低サイクル疲労の破面の特徴を高サイクル疲労と比較して示します。両者とも試験体は同一とし、応力の大きさは異なるものの各変動応力の繰返し数条件はほぼ同じと考えます。まず、き裂進展領域における破面の凹凸について低サイクル疲労では比較的粗いですが、高サイクル疲労では比較的平坦な面を呈します。そして、低サイクル疲労ではき裂進展速度が高サイクル疲労と比べて速いためにビーチマークの間隔も粗くなって数も少ないといった特徴があります。また、低サイクル疲労では負荷応力が大きいために高サイクル疲労と比べて最終破断部が広く残った状態で破壊することになって最終破断部の面積が広くなるといった特徴があります。
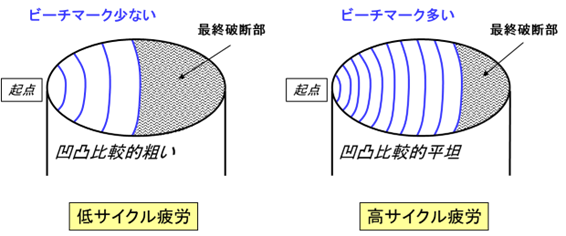
図3 低サイクル疲労の破面の特徴
低サイクル疲労寿命曲線
ここで、応力―ひずみ曲線の各パラメータの定義を図4に示します。
応力―ひずみ曲線はヒステリシスループとなりますが、全体の応力の変化量をΔσ:応力範囲、全体のひずみの変化量をΔεt:全ひずみ範囲と表します。全ひずみ範囲の内、弾性ひずみ範囲の分をΔεe:弾性ひずみ範囲、塑性ひずみ範囲の分をΔεp:塑性ひずみ範囲と表します。また、全ひずみ制御疲労試験ではΔεpおよびΔεeの値として通常、破断繰返し数Nfの1/2の塑性ひずみ範囲および弾性ひずみ範囲を用います。
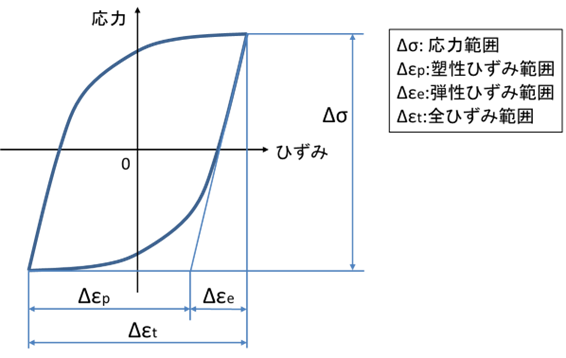
図4 応力-ひずみ曲線の定義
図5は、弾性ひずみ、塑性ひずみおよび全ひずみ疲労寿命の関係を示した図です。ひずみ範囲と破断繰返し数Nfの関係は両対数グラフで表示されます。塑性ひずみ範囲ΔεpとNfの関係は直線表示されることがCoffin-Mansonによって指摘され、多くの金属材料について実証されています。この直線則をCoffin-Manson則といいます。式で表しますと
Δεp·(Nf)^α=Cp (α:疲労延性指数、Cp:疲労延性に関する係数)
一方、弾性ひずみ範囲ΔεeとNfのとの間にも直線則が成り立ち、Basquin則と呼ばれています。式で表しますと
Δεe·(Nf)^β=Ce (β:疲労強度指数、Ce:疲労強度に関する係数)
全ひずみ範囲Δεtは塑性ひずみ範囲Δεpと弾性ひずみ範囲Δεeの和で与えられます。
これらの両対数グラフにおいて塑性ひずみ直線則の傾きの大きさを表すαが0.5–0.7程度であり、弾性ひずみ直線則の傾きの大きさを表すβが0.07–0.12程度であることが知られています。
弾性ひずみ範囲および塑性ひずみ範囲の各直線則が交差する点の繰返し数を遷移疲労寿命と呼び、遷移疲労寿命におけるひずみ範囲の大きさは多くの金属材料においておよそ0.01となることが経験的に知られています。
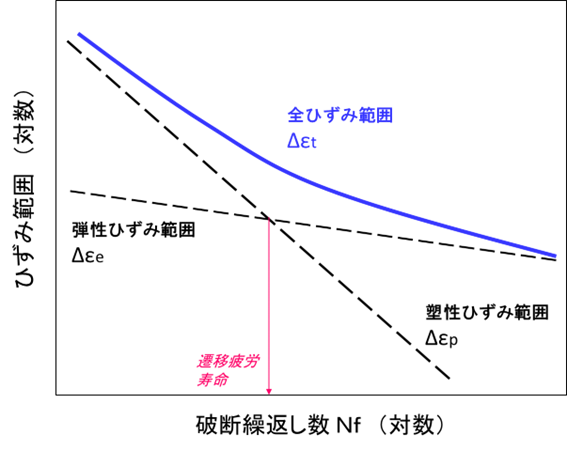
図5 弾性ひずみ、塑性ひずみおよび全ひずみ疲労寿命の関係図
実際の稼働中の機械構造物で得られる応力―ひずみに関する情報は一般的に全ひずみ範囲になります。このため全ひずみ範囲に対する疲労寿命曲線が実用的には有用と考えられます。図6に機械構造用炭素鋼などの一般的な鋼材の低サイクル疲労寿命曲線を例示します。疲労試験は軸方向全ひずみ制御試験で行われ、図中縦軸が全ひずみ範囲、横軸が破断繰返し数です。鋼材の成分や製法によって多種類の鋼材があって強度・延性レベルが大きく異なりますが、低サイクル疲労寿命曲線は概ね図示した線幅の中に分布することが知られています。低サイクル疲労寿命曲線が分布幅の狭い帯状になることから中心線を使って全ひずみ範囲Δεtと破断繰返し数Nとの関係式が求められたりします。低サイクル疲労では破断までの繰返し数が10の4乗から10の5乗程度までです。つまり、10の4乗から10の5乗程度までの繰返し数に相当する全ひずみ範囲では塑性ひずみ範囲が支配的になっているとも言えます。
機械構造用鋼材では一般的に引張強さの高い高強度鋼の方が破断延性は低くなります。破断延性は材料の絞りに関係づけられる指標のことで絞りが大きいほど、すなわち延性なほど破断延性は高くなります。高強度鋼は一般に絞りが小さくなるので破断延性は低くなります。高強度低延性材料は低強度高延性材料と比べて、全ひずみ範囲が大きい領域では破断寿命が短くなる傾向があり、逆に全ひずみ範囲が小さい領域では破断寿命が長くなる傾向があります。全ひずみ範囲の大きい領域、すなわち塑性ひずみが支配する低サイクル疲労では材料の延性を改善することが破断寿命の長寿命化に有効です。
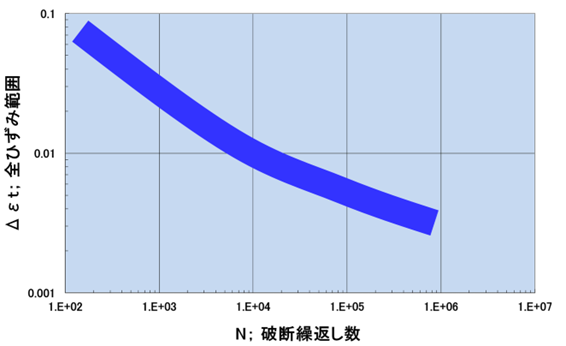
図6 一般的な鋼材の低サイクル疲労寿命曲線
疲労強度に関連する以下のねじ締結技術ナビ技術資料・コンテンツもあわせてご覧ください。