S-N曲線について
金属疲労は金属材料を用いた部材の破壊原因の多くを占めています。この疲労破壊防止には設計段階で金属材料、部材の使用環境下での寿命予測が当然必要になりますが、この設計のための基本的な試験データがS-N曲線であります。金属部品や製品の耐久性試験も一般的に行われますが、定量的な評価解析には対象となる製品部位のS-N曲線が必要です。S-N曲線を求める試験は疲労試験機で行われますが、ここでは10の4乗(10,000サイクル)オーダー以上の繰返し数で疲労破壊する高サイクル疲労試験の場合について述べます。なお、ねじ締結技術ナビ「疲労試験の仕方(金属疲労)」についても参照してください。
図1は、S-N曲線の役割を簡単に述べたものですが、S-N曲線を使った疲労の予測には、疲労寿命予測と疲労強度予測があります。①疲労寿命予測は想定される応力下で耐えられる繰返し数の予測であり、②疲労強度予測は特定の繰返し数に対して耐えられる応力の予測になります。
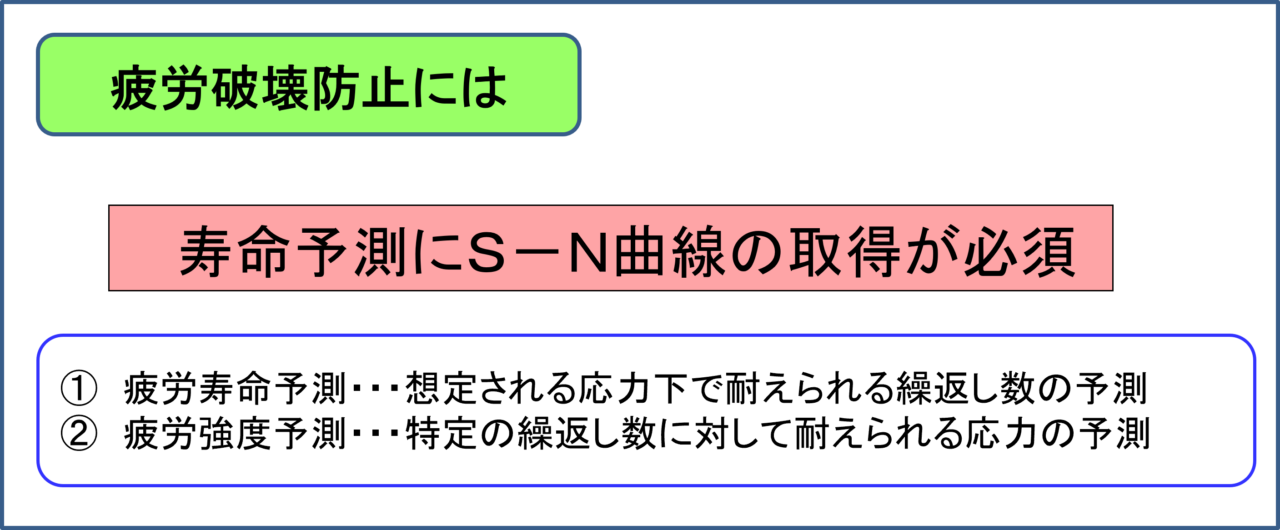
図1.S-N曲線の役割について
試験材の準備
試験材についてはテストピース試験片を作製する場合、実機材料からの切り出し試験材を作製する場合、また実機部品そのものを試験材とする場合などがあります。テストピース試験片の形状は任意ですが、JISZ2273「金属材料の疲れ試験方法通則」では円形断面又は板状とすることが原則になっています。平滑材とする場合は、細かい粒度の研摩や縁部の適切な丸みが必要になります。また、当然ですがチャック部の断面積を十分大きく取った形状になります。実機材からの切り出し試験材の作製では、試験機における荷重負荷方向が実環境下での当該部位にかかる応力方向と一致するようにチャック部の形状を考慮して切り出すことになります。小型部品では手動で切り出すこともあります。切り出し作業で当該部位を挟んだりすることはキズを付ける懸念がありますので避けることが望ましいです。実機部品を疲労試験する場合は治具を作製し、治具を介して試験材を試験機に取り付ける必要があります。治具の設計では先と同様、試験機における荷重負荷方向が実環境下での当該部位にかかる応力方向と一致するようにしなければなりません。
試験条件の設定
疲労試験には試験材に対する荷重負荷方向の違いから引張圧縮、回転曲げ、平面曲げ、ねじりといった各種の試験方法があります。ここでは最もよく試験されている引張圧縮疲労試験に着目して説明します。
試験条件の設定について重要な部分を図2に示します。内訳として荷重(変位)条件の設定、試験周波数の設定、リミット値の設定があげられます。なお、ひずみ制御で行われる低サイクル疲労試験ではひずみ振幅条件の設定が必要になりますが、ここでは触れません。
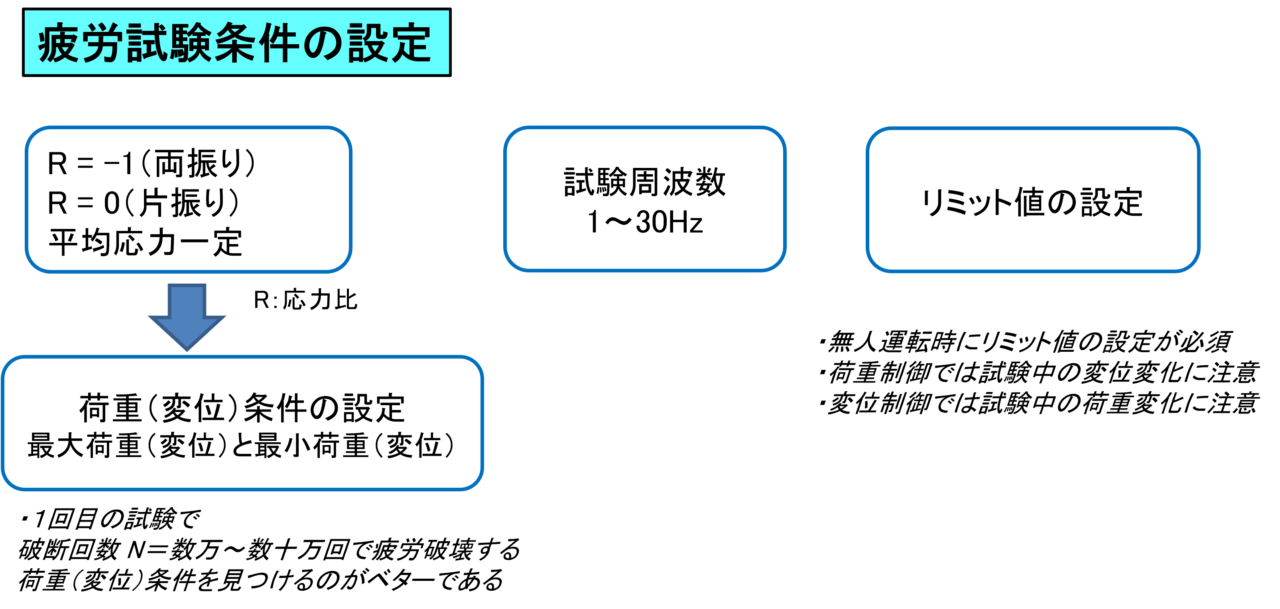
図2.試験条件の設定内訳
一般にS-N曲線の測定では両振り、片振り、平均応力一定のいずれかの条件で試験されます。実機の負荷応力状態がいずれであるかを判断して選ぶことになります。その後、試験機で負荷する荷重条件、または変位制御の場合は変位条件を設定します。ここで1回目の試験で破断回数(破断するまでの繰返し数)Nが数万回から数十万回程度で疲労破壊する条件であれば2回目以降の荷重(変位)条件の設定が容易になります。
図3に各種の応力条件とS-N曲線のイメージ図を示します。両振りである応力比R=-1、片振りである応力比R=0、平均応力σm=一定値の場合のS-N曲線が示されています。片振りの試験ではR=0では最低荷重のばらつきによって圧縮側に荷重がかかる懸念がありますので、R=0~0.1の範囲の値にすることが多いです。これらのS-N曲線において疲労限度はR=-1の場合が最も大きく、片振りのR=0.05では疲労限度がやや低下します。平均応力が一定値の条件では平均応力が大きくなるにつれて疲労限度線図(ねじ締結技術ナビ「平均応力の影響(金属疲労)」参照にしたがって疲労限度が低下します。
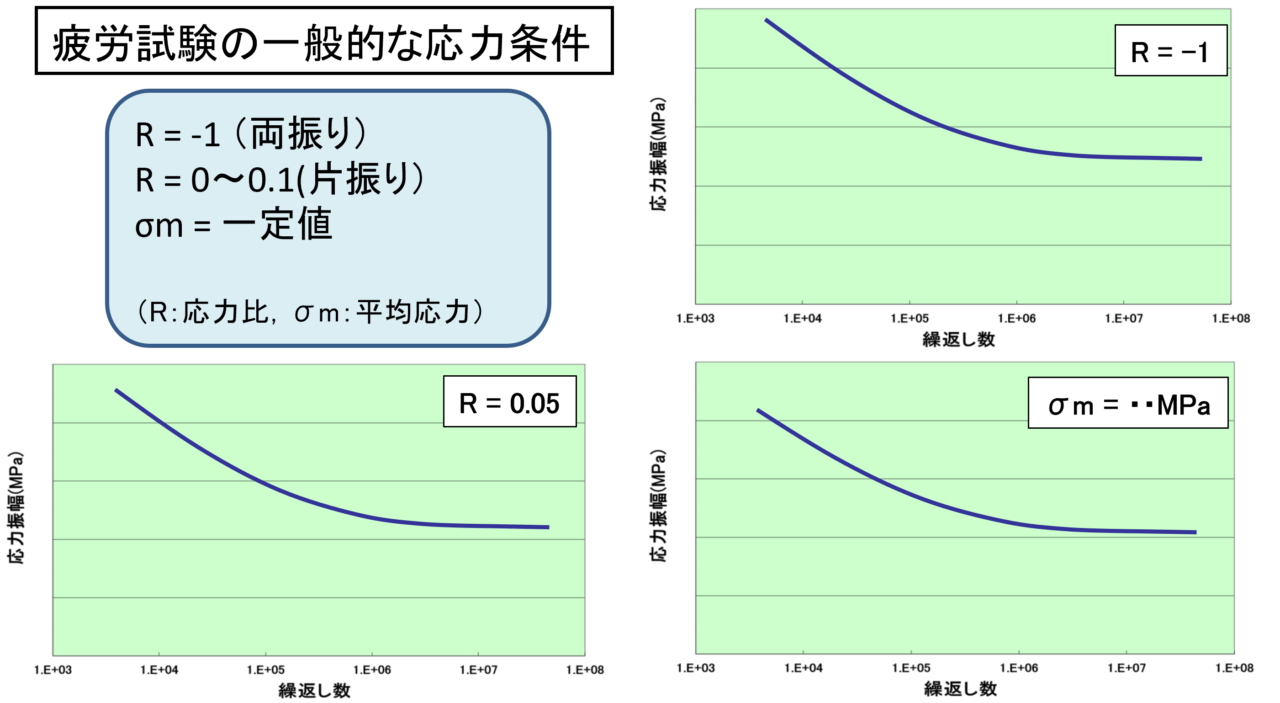
図3.一般的な応力条件とS-N曲線のイメージ
試験周波数の設定では試験時間の短縮から10~20Hz程度で試験することが比較的多いと思われます。図4は疲労強度に及ぼす試験周波数の影響の概略です。試験周波数が高くなると試験材の振動による発熱で温度が高くなって疲労強度に影響することが考えられますが、100Hz程度までは疲労強度はほぼ変化しないといわれています。また、通常の疲労試験機の周波数範囲も100Hz程度までが一般的です。ギガサイクル疲労試験に対応する超音波疲労試験機では試験周波数が20kHzを超えますが、高速振動による発熱を防止するために強制空冷装置などが付属しています。
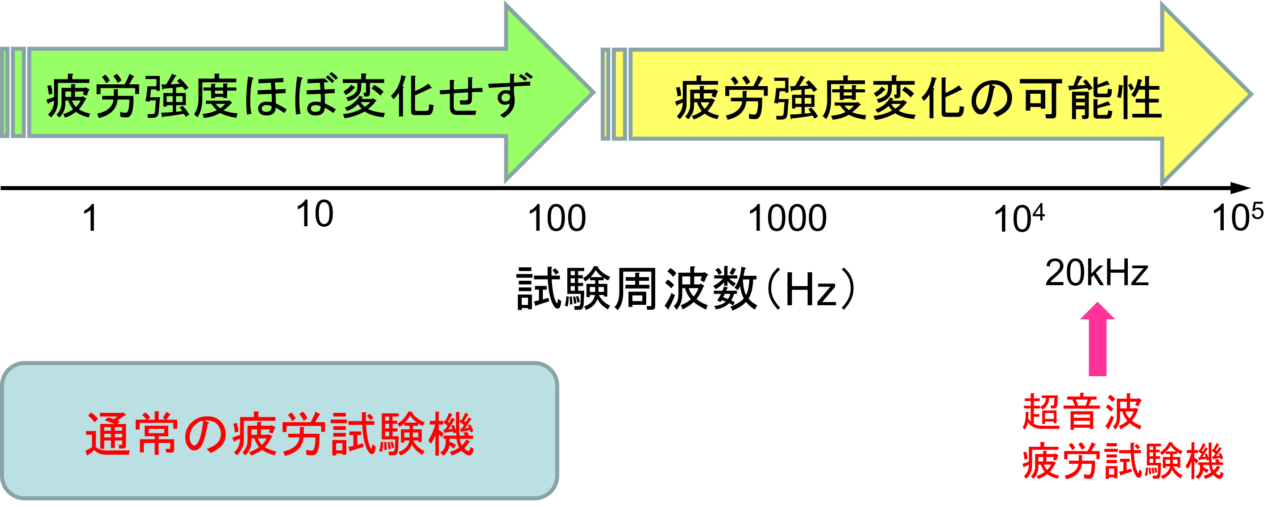
図4.試験周波数の影響について
試験条件の設定において、長時間の疲労試験は無人運転で行われることから試験開始時に通常リミット値の設定を行い、試験材の破断時に自動で停止させて破断回数Nを保持します。試験が荷重制御の場合は最大荷重よりやや大きい荷重値、および最小荷重よりやや小さい荷重値をリミッット値として設定します。試験が変位制御の場合は最大変位よりやや大きい変位値、および最小変位よりやや小さい変位値をリミット値として設定します。ただし、試験材が破断すると荷重や変位が大きく変動する懸念から安全策として通常は荷重および変位の両者に対してリミット値の設定を行います。
また、疲労試験の進行とともに荷重制御では変位量が、変位制御では荷重が大きく変化する場合もあります。リミット値の設定が適切でないと試験中に思いがけなく停止してしまうことになります。試験材が疲労試験の進行によって疲労破壊までどのように変化するか予測しておくことも大切です。
疲労試験のポイント
試験材が準備できて試験条件が設定されれば、試験材を疲労試験機に取り付けて試験開始です。手順については、ねじ締結技術ナビ「疲労試験の仕方(金属疲労)」に掲載していますので参照してください。
ここでは試験材の取付けに関して参考となる事例を紹介したいと思います。
一般的なテストピースやねじ・ボルトなど対称性の高い実機材では、試験材の中心線が試験機チャック部の中心位置になるように、すなわち軸心が一致するように取り付けます。治具を設計する場合でも比較的容易と考えられます。一方、非対称の一般的な形状の実機材では、実際の使用環境下での応力負荷方向が試験機での軸心と一致するように治具を設計するのが望ましいと考えられます。
次に、試験材チャックの参考事例として厚みの異なる二枚板試験材、およびワイヤ試験材の各場合について図5に示します。
図5(a)は厚みの異なる二枚板がそれぞれリベットで締結された試験材です。この引張圧縮疲労試験では最終的にリベット本体あるいは板材のリベット孔のどちらかが疲労破壊します。実機においては二枚の板材の接触面において接触面と並行方向に応力が繰り返されます。疲労試験ではその接触面が軸心になるように取り付けるため、各板材と同一厚さのスペーサーとなる当て材を用意し、図のように設置して上下でチャックします。これによって実際の応力負荷状態を試験機で安定して模擬することができます。
図5(b)は硬鋼線などのワイヤの試験材です。ワイヤを両端で直接チャックして試験しますと通常はチャック部で破壊して正しい試験結果が得られません。このため例えば試験材のチャック部の断面積を増やしてチャック部での疲労破壊を防ぐ工夫が必要になります。JIS G 3525「ワイヤロープ」では引張試験機への取付け方法として、試験片の両端をホワイトメタル、亜鉛などで円すい形に固める方法、又はこれに代わる適切な方法で取り付けることが規定されています。疲労試験でも同様にワイヤの両端部分に円すい枠を設けて低融点金属を鋳造し、ソケットとも呼ばれる円すい形のチャック部を設けたりします。一方、参考事例ですが、硬鋼線の疲労強度は表面粗さによって大きく異なり、表面が平滑になると疲労強度が向上します。この違いを利用して、チャック部の素線表面を緻密な研磨紙で断面積への影響を無視できる程度で研磨し、その後アルミ箔を幾重にも巻き付けてチャックする方法で、チャック部での破断を防止できる場合もあります。また、別の方法ですが、大きめのプーリーを2個用意してそれぞれにワイヤを巻き付けて、2個のプーリー間のワイヤ試験材が軸心と一致するようにプーリー部をチャックする方法もあります。
ワイヤの疲労試験でチャック破断する場合は、疲労試験回数を増やして適切な位置で破断した場合のみ疲労データとして採用します。
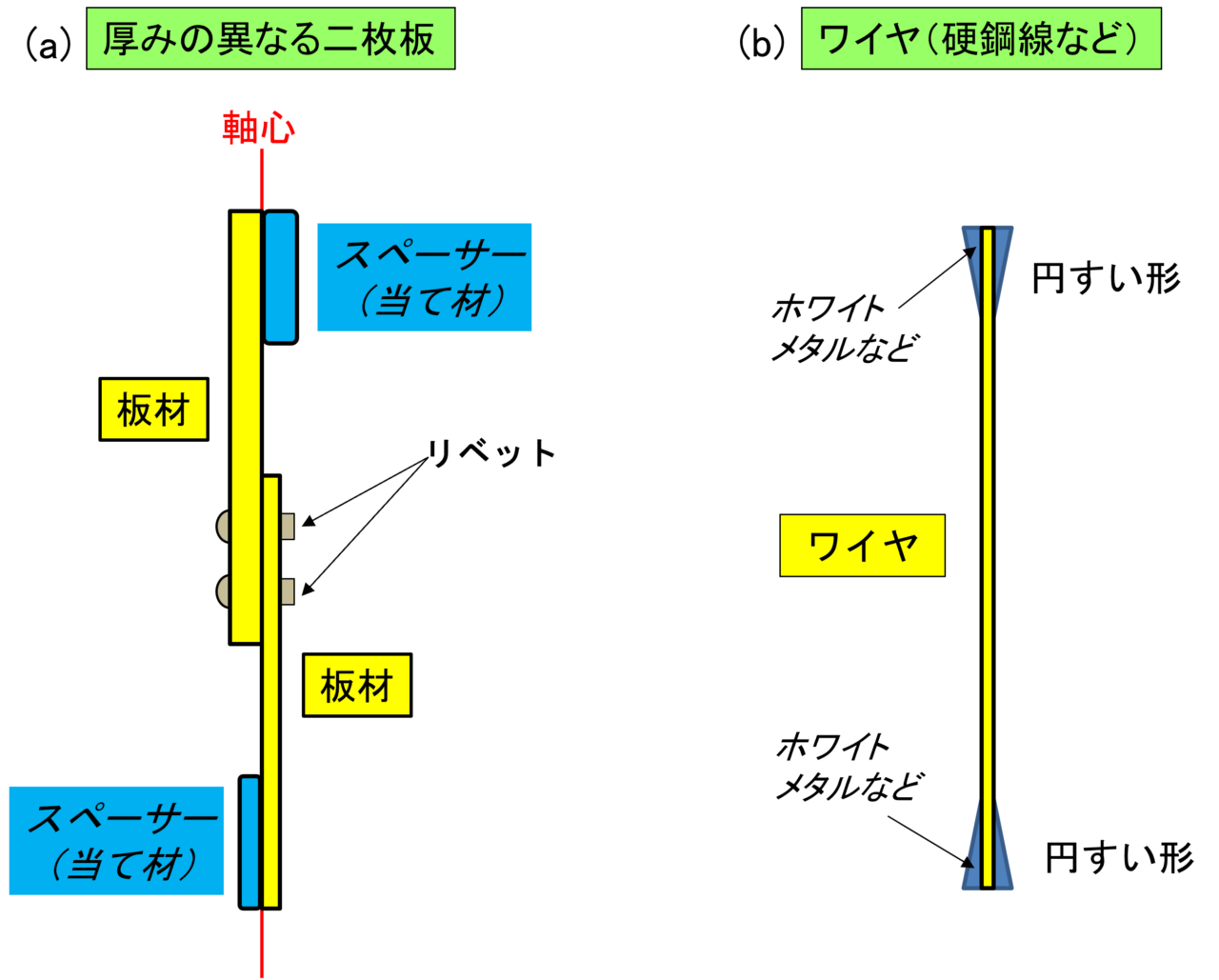
図5.試験材のチャックの事例
疲労強度に関連する以下のねじ締結技術ナビ技術資料・コンテンツもあわせてご覧ください。