非鉄金属材料の疲労の特徴
非鉄金属材料は鉄鋼材料と比べてコスト的に高いものが多いですが、アルミニウム(比重2.7)やチタン(比重4.5)のような軽量で強度と耐食性を併せ持った材料は各種分野で構造用材料としても使用されています。例えば熱処理によって強度を高めたアルミニウム合金は軽量で耐食性も優れることから、航空機分野で長年使われています。最近ではチタン合金がその優れた比強度(密度当たりの引張強さ)性能から先端産業分野で構造用材料としての利用が広まっています。一方、銅では純銅が優れた導電性から電線ケーブルとして使用されており、また銅合金が優れた耐食性と加工性から各種機械部品や船舶用プロペラ(主に黄銅とアルミニウム青銅)として多用されています。
金属材料を用いた機械製品・部品では金属疲労に対する安全設計が必要です。非鉄金属材料についても構造用として使われる場合は当然のことながら疲労に対して安全性(耐久性)が保証されなければなりません。また、銅線ケーブルにおいては装着されている機械製品が振動するケースでは銅線そのものについて疲労に対する注意(安全設計)が必要になります。ここでは、非鉄金属材料としてアルミニウム、銅、およびチタンを取り上げ、その疲労の特徴を主にS-N曲線に関して概説します。
金属疲労に対する安全設計の考え方は非鉄金属材料でも鉄鋼材料でも基本的に同じです。材料の疲労強度を表すS-N曲線と実働負荷応力の関係で検討されます。疲労強度の大きさは材料の引張強さにおよそ比例します。アルミニウムや銅は概ね引張強さはそれほど高くはありませんが、高強度銅合金や高強度チタン合金では引張強さが1000 MPaを超えるものがありますので、それらの疲労強度は鉄鋼材料と比べて同等に高い値になります。図1に、アルミニウム、銅、およびチタンのS-N曲線の特徴を示します。
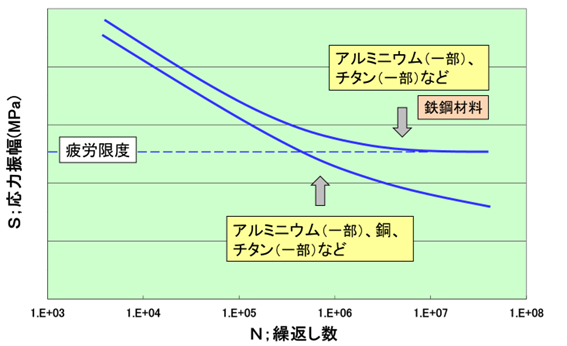
図1 非鉄金属材料のS-N曲線の特徴
鉄鋼材料では図1にも示しましたように、S-N曲線は繰返し数の増加とともに右下がりの曲線が10の6乗から10の7乗あたりで折れ曲がり、その後はほぼ水平になって疲労限度といわれる水平部分が存在します。一方、非鉄金属材料では一般的には疲労限度が存在しないといわれており、繰返し数10の7乗の時間強度を便宜的に疲労限度の値にしています。ただし、一部のアルミニウム合金やチタン合金では繰返し数10の7乗あたりから疲労強度の低下が極めて緩やかになってほぼ水平ともいえるS-N曲線になります。
非鉄金属材料の疲労強度
非鉄金属材料として、アルミニウム、銅およびチタンの各金属について疲労強度を述べたいと思います。なお、疲労強度の大きさを引張強さに対する比率としてよく表されますが、非鉄金属材料の場合でも鉄鋼材料と比べて特に特徴的なことはありません。例えば、引張圧縮疲労では両振りで比率はおよそ0.4–0.5程度となっており、鉄鋼材料の場合と大きな差はありません。一方、疲労破壊現象のメカニズムに関しては、鉄鋼材料の場合と比べて、繰返し応力によってき裂が進展していくという基本的な考え方は同じですが、き裂先端開口部でき裂の発生が止まって進展が途中で停滞する停留き裂現象の発生に関しては異なるようです。
アルミニウムおよびアルミニウム合金の疲労強度
アルミニウム合金としてAl-Mg系の展伸材であるA5052P-H34材(引張強さ240 MPa)およびAl-Si-Cu系のダイカスト材であるADC12(引張強さ260 MPa)について室温で実測したS-N曲線を図2に示しました。疲労試験は軸引張圧縮で両振り(応力比R=-1)で行いました。なお、Pは製品形状で板を表し、またH34は質別記号で、冷間加工(1/2硬質)を行いさらに安定化処理を施したものです。
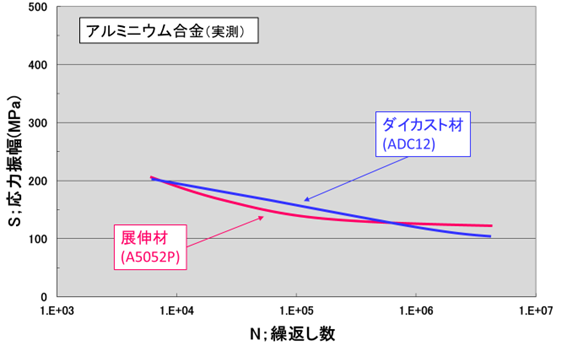
図2 アルミニウム合金(展伸材およびダイカスト材)のS-N曲線の例
A5052は冷間加工によって加工硬化する非熱処理型の合金で、マグネシウムの添加によって強度と耐食性を向上させたものです。この材料はアルミニウム展伸材の中で切削性と加工性が非常に優れており最も一般的なアルミニウム材です。またADC12は機械的性質、切削性、鋳造性に優れることからアルミニウム合金ダイカスト材の中で最も主流となる材料で自動車部品などに多く使われています。
図2に示されるように展伸材のA5052PのS-N曲線は10の6乗から10の7乗の繰返し数付近ではほぼ水平の線になるのに対し、ダイカスト材のADC12のS-N曲線は繰返し数が10の6乗を超えても右下がりに低下していきます。この例のようにアルミニウム合金のS-N曲線は疲労限度を示す水平部が存在するケースもあるようです。アルミニウム合金では熱処理型合金であるAl-Cu系合金は一般的に疲労限度を示さずに繰返し数とともに右下がりのS-N曲線になりますが、非熱処理型合金であるAl-Mg系合金のような加工硬化性が高い材料の場合には疲労限度に相当する水平部が存在するS-N曲線になる可能性があるようです。
疲労限度はき裂の進展が停止する現象である停留き裂の発生が原因と考えられており、停留き裂の挙動に微視組織が影響します。Al-Mg系合金のように加工硬化性が高く、冷間加工後に時効硬化する現象であるひずみ時効を併せ持つ材料ではき裂先端部で硬化しやすくなってき裂の停留を安定化させている可能性が考えられます。
高強度アルミニウム合金の最高強度は実用レベルでは引張強さがおよそ700 MPa程度です。ねじ部品に用いられるアルミニウム材としては、純アルミは強度が低いのであまり使用されませんが、Al-Mg系の5000番台合金、およびAl-Mg-Zn系の7000番台合金が一般に使用されており、特にA5052やA5056などの5000番台合金は加工性、耐食性、熱伝導性に優れており非磁性でもあることから多用されています。
銅および銅合金の疲労強度
銅および銅合金の例として純銅の無酸素銅であるC1020BD材(引張強さ400 MPa)およびタフピッチ銅であるC1100BD材(引張強さ390 MPa)、および快削黄銅のC3604BD材(引張強さ460 MPa)について室温で実測したS-N曲線を図3に示しました。疲労試験は軸引張圧縮で両振り(応力比R=-1)で行いました。なお、BDは引抜棒を示す記号です。また、質別記号については、純銅の両者がともに記号Hで、ある程度まで加工硬化によって強度を高めたものですが、快削黄銅は記号Fで製造のままのものです。
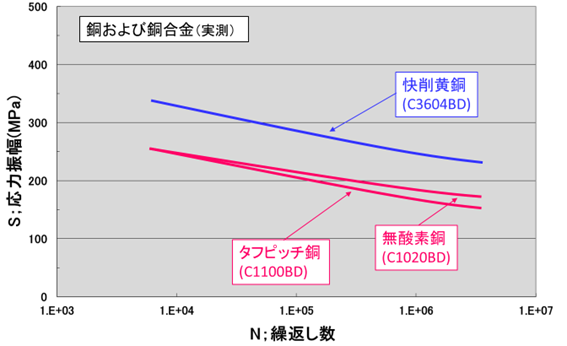
図3 銅および銅合金のS-N曲線の例
図3に示されるように純銅および快削黄銅ともにいずれもS-N曲線は繰返し数が10の6乗を超えても右下がりに低下して水平部は存在しませんでした。また、純銅同士では引張強さがやや高い無酸素銅の方が疲労強度もやや高い結果が得られました。
図4に無酸素銅棒材(C1020BD)について疲労試験によって破壊した破断面のマクロ観察結果(マクロ破面)を示しました。破面に垂直方向に引張圧縮荷重が繰返し加わって疲労破壊しています。疲労破壊した無酸素銅のマクロ破面では弧を描いた縞模様であるビーチマークが比較的よく観察され、円弧の中心方向が起点の方向に一致します。また、起点からき裂進展方向に沿っていわゆるき裂進展模様も観察することができます。
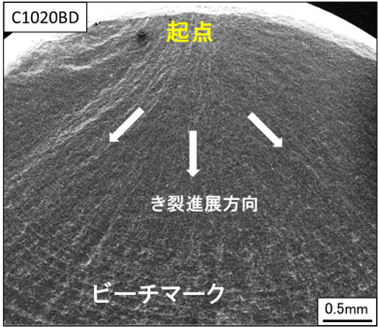
図4 無酸素銅棒材の疲労破壊のマクロ破面
高強度銅合金(銅チタン合金など)の最高強度は引張強さが1000 MPaを超えていますが、ねじ部品に用いられる銅材料としては一般に従来からの銅材料が主に電気部品用途などに使われています。純銅ねじとして無酸素銅が特殊用途向けに、タフピッチ銅が一般向けに使用されています。また合金では黄銅(C2000番台)、快削黄銅(C3000番台)が多用されています。これらの銅材は耐食性、加工性、電気伝導性、熱伝導性、非磁性といった優れた特長を有しています。
チタンおよびチタン合金の疲労強度
チタン材料について疲労強度の実測はしておりませんが、代表的な(α+β)型チタン合金であるTi-6Al-4V合金について室温におけるS-N曲線の推定図を図5に参考例として示しました。ここでαはチタンの低温相を、βはチタンの高温相を意味し、(α+β)型は両者の相が室温で共存した組織になっています。疲労強度は軸引張圧縮で両振り(応力比R=-1)を想定しています。本合金は熱処理の違いでミクロ組織が大きく変化し、機械的強度も大きく変化します。ここでは引張強さが1000 MPaクラスの材料を想定しました。一般的に本合金のS-N曲線は10の6乗から10の7乗の繰返し数付近でほぼ水平の線になることが知られています。またその疲労限度はミクロ組織の違いによって影響されますが、引張強さのおよそ1/2に想定し、引張強さが1000 MPaクラスでは疲労限度がおよそ500 MPaクラスになると想定しています。図5はこの考え方で表したS-N曲線になります。チタンおよびチタン合金では熱処理や加工処理によってミクロ組織や微視組織が変化し、この影響で疲労強度の変化のみならずS-N曲線に疲労限度を示す水平部が存在するかどうかも変わる可能性があります。
チタン材の比重は4.5前後、引張強さは純チタンでおよそ300–700 MPa、チタン合金でおよそ600–1200 MPaと比強度が高い材料です。ねじ部品に用いられるチタン材としては、チタンは比強度が高く耐食性に優れかつ非磁性であるため、航空機用、医療用などの特殊分野で使用されています。コストが高く成形がやや難しいので一般用のねじには向きません。チタン材として純チタン(JIS 2種)およびTi-6Al-4V合金(JIS 60種)が比較的多く使用されています。Ti-6Al-4V合金ねじの引張強さは900 MPa以上と高強度です。
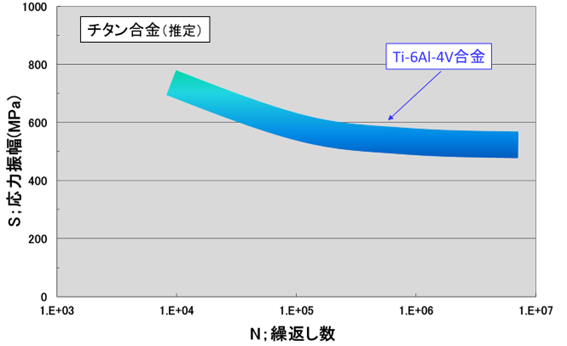
図5 チタン合金のS-N曲線の推定例
疲労強度に関連する以下のねじ締結技術ナビ技術資料・コンテンツもあわせてご覧ください。