表面効果について
金属疲労は表面から疲労破壊が始まることが大半で、機械加工、熱処理、表面処理などによって表面に形成される加工層が疲労強度に著しく影響を及ぼします。すなわち、疲労強度は材料の表面状態によって大きく影響されます。機械加工によって発生する表面粗さ(表面凹凸)によって疲労強度は変化し、表面粗さが大きくなると疲労強度は低下します。表面硬さの増加、および圧縮の表面残留応力の発生は疲労強度の増加に有効です。なお、塑性加工によって生じた残留応力は疲労過程の進行とともに減少し、疲労限度に対する影響も小さくなっていくことに注意が必要です。
表面処理方法として、高周波焼入れ、窒化、ショットピーニングなどの表面処理は疲労強度を増加させるのに有効です。浸炭は表面硬化させますが、合金中の元素による酸化物の形成で疲労強度が低下する場合もあるので注意が必要です。めっき処理は大気中の疲労強度に対しては低下させますが、腐食環境中の腐食疲労に対しては疲労強度向上に有効です。
表面状態の差による疲労強度の変化率は表面係数(表面効果係数)で示されます。表面状態が変化した材料の疲労強度と特別な表面処理を施さない平滑材(粗さ1μm以下)の疲労強度の比率を表面係数といいます。
図1に疲労に及ぼす表面状態の影響を簡潔に示しました。
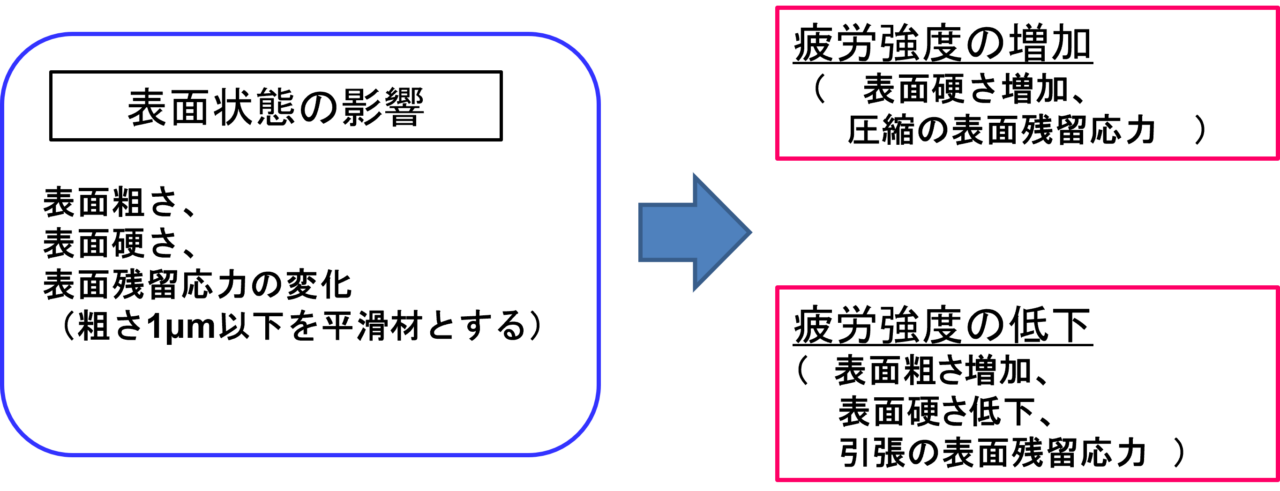
図1.疲労に及ぼす表面状態の影響
表面仕上げの影響
機械的な表面仕上げ方法として切削、研削、研磨などがあります。この表面仕上げによって材料表面には冷間加工による硬化、加工疵による表面粗さ(表面凹凸)、残留応力の発生が起こります。冷間加工による硬化は疲労強度の増加、表面粗さの増加は疲労強度の低下、引張の残留応力は疲労強度の低下、圧縮の残留応力は疲労強度の増加につながります。これらの要素が複数絡むと表面仕上げ加工による疲労強度の変化は多様になります。
切削や研削、研磨では表面粗さの大きさによって疲労強度は変化しますが、引張の残留応力が発生することもあってその場合は想定以上に疲労強度が低下することもあります。熱間圧延、熱間鍛造による黒皮材料では表面粗さに起因する疲労強度の低下のみならず、表面脱炭層形成によって引張の残留応力が発生して疲労強度が大きく低下することが知られています。
加工硬化と残留応力の発生といった影響が無い場合、疲労限度は表面粗さによって変化します。図2は金属部材の表面粗さと表面係数の関係を模式的に示したものです。表面の凹凸が一種の切欠き作用を持つと考えられ、表面粗さが大きくなるほど疲労強度は低下します。表面粗さによる疲労強度低下への影響度は材料の引張強さが大きいほど低下率も大きくなります。図中では引張強さが材料A>材料B>材料Cの順に変化しています。
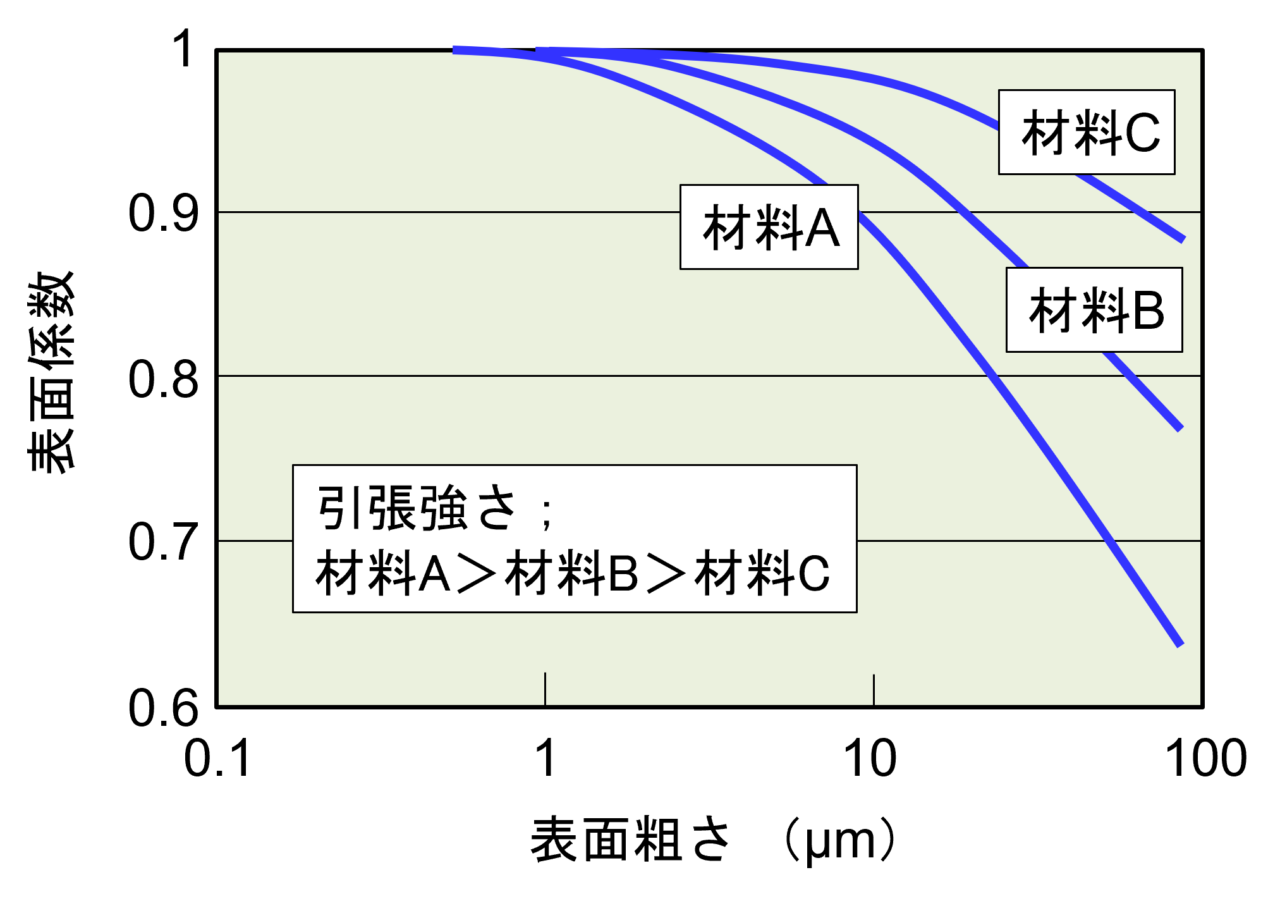
図2.表面粗さと表面係数の関係
表面処理の影響
高周波焼入れは急速加熱によって材料表面を急加熱後急冷する熱処理方法で、表面層が硬化されます。表面硬化と同時に圧縮の残留応力も発生することで疲労強度が大きく増加します。
圧縮残留応力の大きさは鋼種や焼入れ深さによって変化します。高周波焼入れ後の焼戻し温度が高いと圧縮残留応力の大きさが低下するので疲労強度特性向上の目的の場合は低温焼戻しが推奨されます。
図3は高周波焼入れ材について表面のビッカース硬さと疲労限度を推定した図です。疲労き裂は一般に表面から発生し、表面層の硬さが疲労限度に大きく影響します。図では表面層のビッカース硬さから引張強さに換算し、回転曲げ疲労では引張強さの50%、引張圧縮疲労では引張強さの40%の値を疲労限度の基準の大きさとし、さらに圧縮残留応力による疲労限度の増加を考慮してやや高めに位置する曲線としています。この場合、厳密には高周波焼入れ材では中心部分を柔らかいままに保って靭性を持たせますので、その分疲労寿命が減少する可能性がありますので圧縮残留応力による疲労限度の向上分をやや小さめに見積もっています。
なお、引張強さは材料全体の静的な強度を表しますので、内部が柔らかい高周波焼入れ材では表面層のビッカース硬さから推定される引張強さの値よりも小さくなると考えられます。
高周波焼入れは疲労限度を向上させる有効な表面処理方法です。
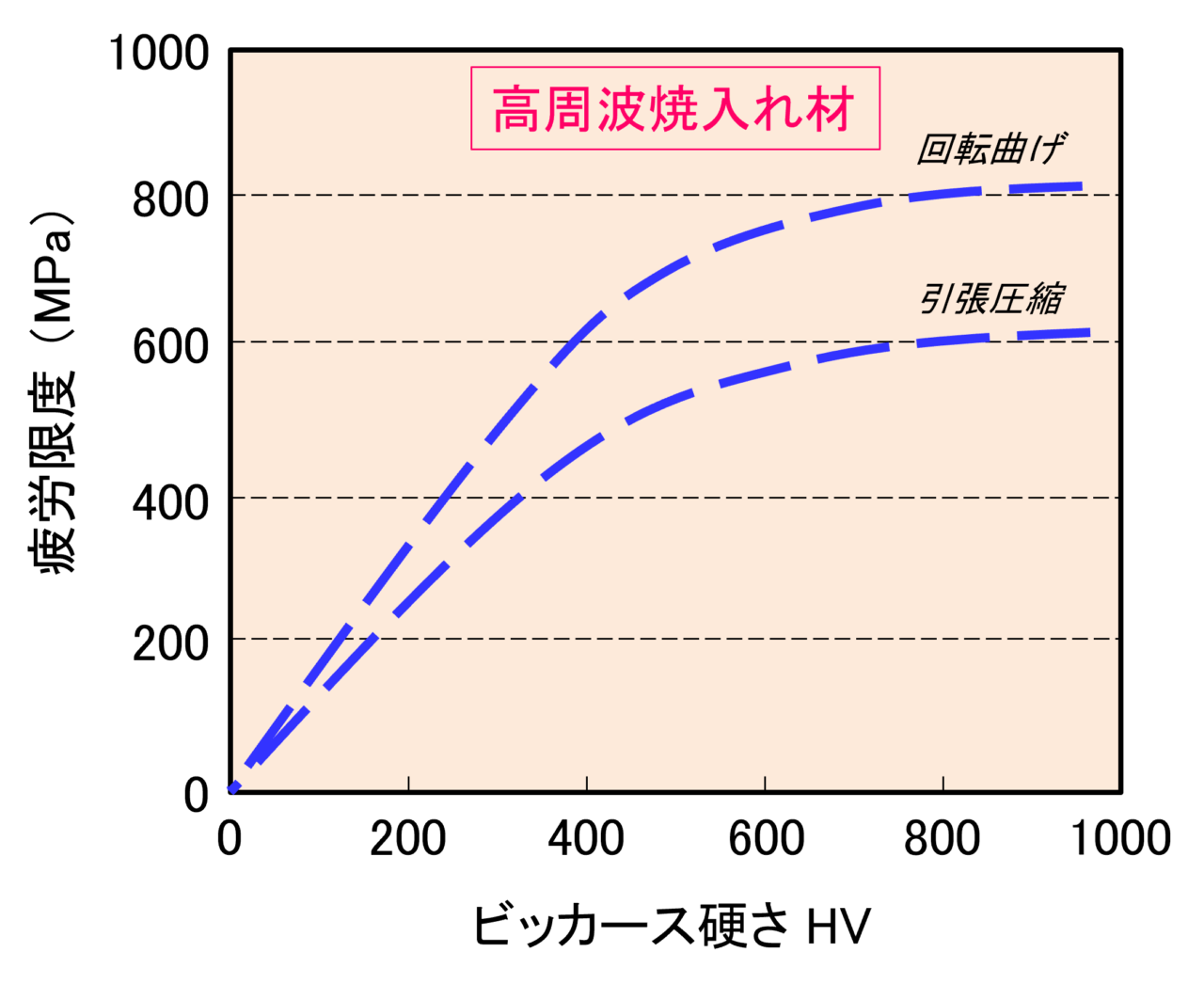
図3.高周波焼入れ材の表面硬さと推定疲労限度
表面処理に浸炭という方法があります。浸炭は900℃域のオーステナイト域で低炭素鋼に外部から炭素を進入させて表面層を高炭素(1%程度)にする処理方法です。その後、焼入れ焼戻しによって表面層が高硬度のマルテンサイト相になります。真空浸炭法では表面硬化によって疲労強度の改善が期待されますが、大気中で処理されるガス浸炭法では、鋼中の合金元素であるSi、Cr、Moなどが表面近傍の粒界に沿って酸化物を形成するとともに焼入れ不完全現象を起こし、疲労強度は逆に低下することがあります。
窒化処理は500~600℃の温度域で外部から窒素を進入させ、鉄窒化物や窒素固溶体を形成して高い表面硬さを得る方法です。表面の高硬度の効果で疲労強度も改善されます。図4は窒化処理による疲労限度の増加を模式的に示したものです。
ガス窒化法では表面硬さがHV1000以上と非常に高く、耐摩耗性改善の点では非常に優れますが、処理時間が40~100時間とかなり長いことから、疲労強度特性向上のためには軟窒化と呼ばれる方法がとられています。これは、表面硬さをHV600~800程度として硬化層も浅くした処理方法で、塩浴窒化法や混合ガス軟窒化法があり、処理時間も数時間と短時間です。疲労強度特性改善のためにはこの程度の表面硬さでも十分高く、圧縮残留応力の発生もあってガス窒化法と同レベルの疲労強度改善効果があります。
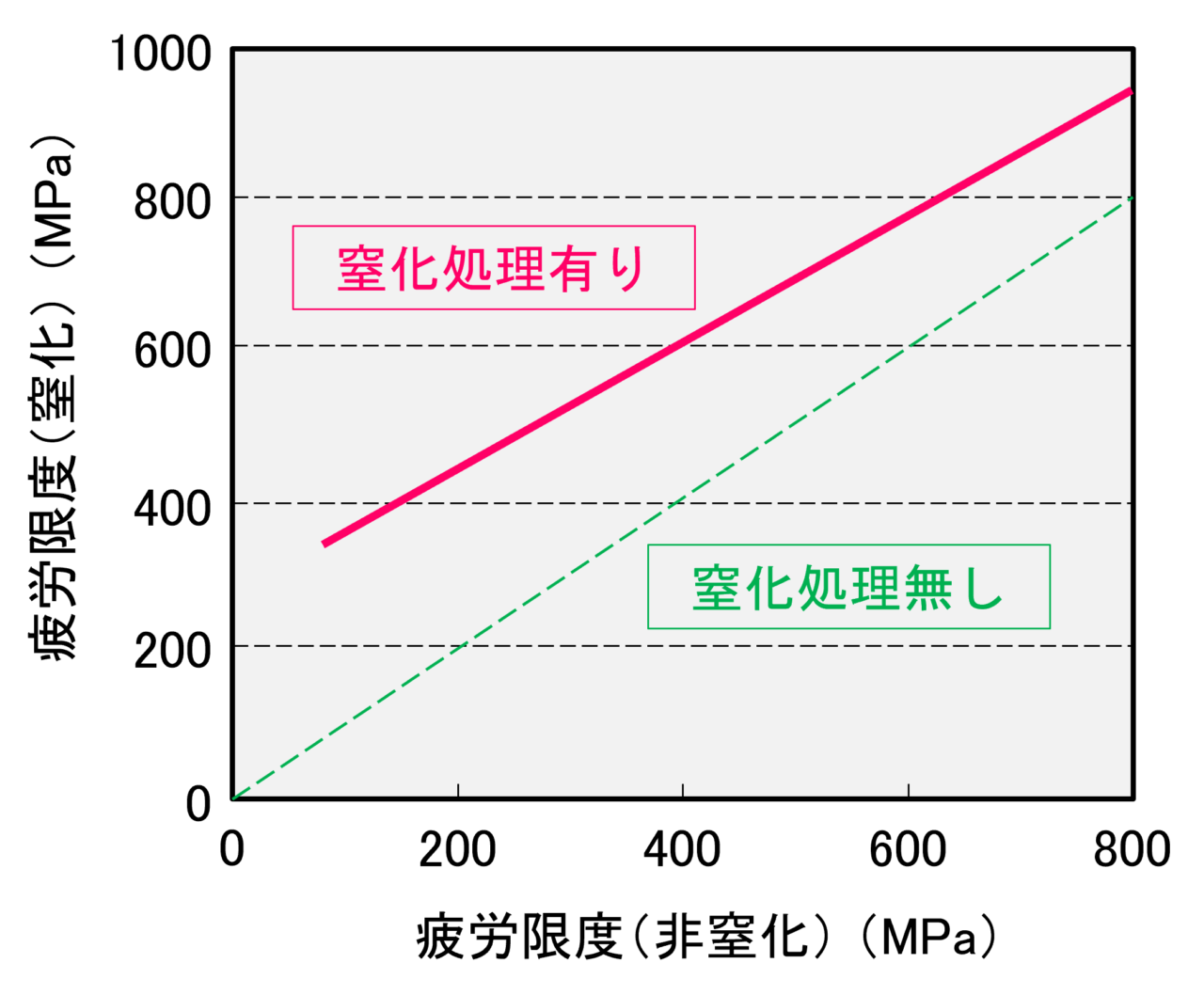
図4.窒化処理による疲労限度の増加
表面ロール加工は塑性加工を表面層に限定して施す方法で表面層が加工硬化し、さらに加熱しながら塑性加工を加えるとひずみ時効によって表面硬さが上昇し、圧縮残留応力も発生して疲労強度が大きく改善されます。
次に、ショットピーニングは疲労強度特性を大きく改善します。ショットピーニングとは直径1mm程度の剛球を材料表面に高速で投射し、表面に加工硬化や圧縮残留応力を付与する加工方法で、炭素量が多い高強度の材料ほど圧縮残留応力が大きくなり疲労強度の増加も大きくなります。疲労強度と耐摩耗性向上の目的で広く使用されており、特にピアノ線や硬鋼線を用いたコイルばねの疲労強度改善には非常に有効な表面処理方法です。図5はショットピーニングの有無によるS-N曲線の変化を模式的に示した図で、疲労限度がおよそ50%程度まで増加します。
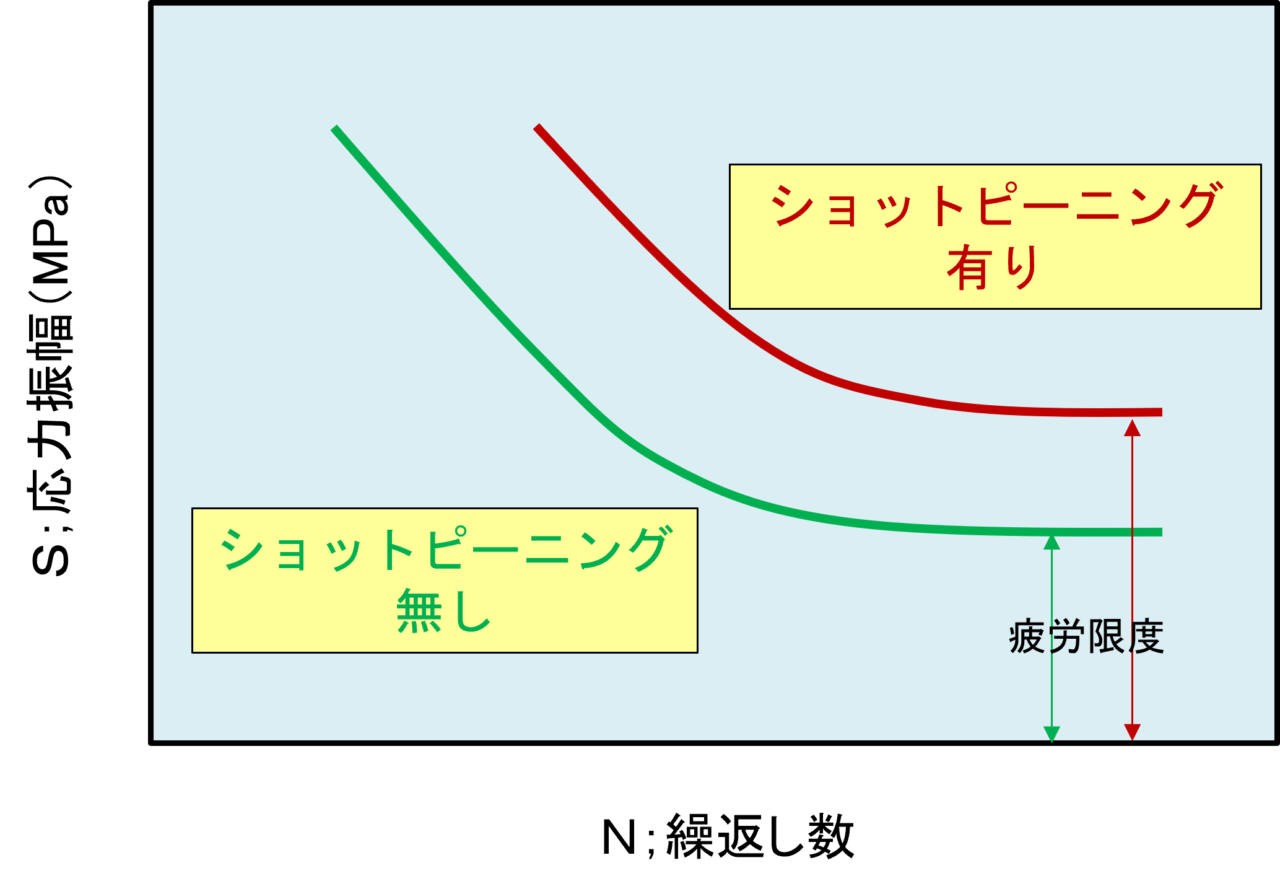
図5.ショットピーニングの有無によるS-N曲線の概念図
めっきは大気中の疲労限度が低下することが多いです。影響の度合いはめっき条件、使用環境、材料強度によって異なります。逆に、腐食環境下ではその耐食性のために疲労限度の改善に効果があります。
図6は電気亜鉛めっきと溶融亜鉛めっきの両者について疲労限度に及ぼすめっきの影響を表したイメージ図です。電気亜鉛めっきでは疲労限度は殆ど変化しませんが、溶融亜鉛めっきでは材料が高強度側になると疲労限度が低下します。なお、腐食環境下では亜鉛めっきの犠牲防食作用のために腐食疲労強度を改善する効果があるといわれています。
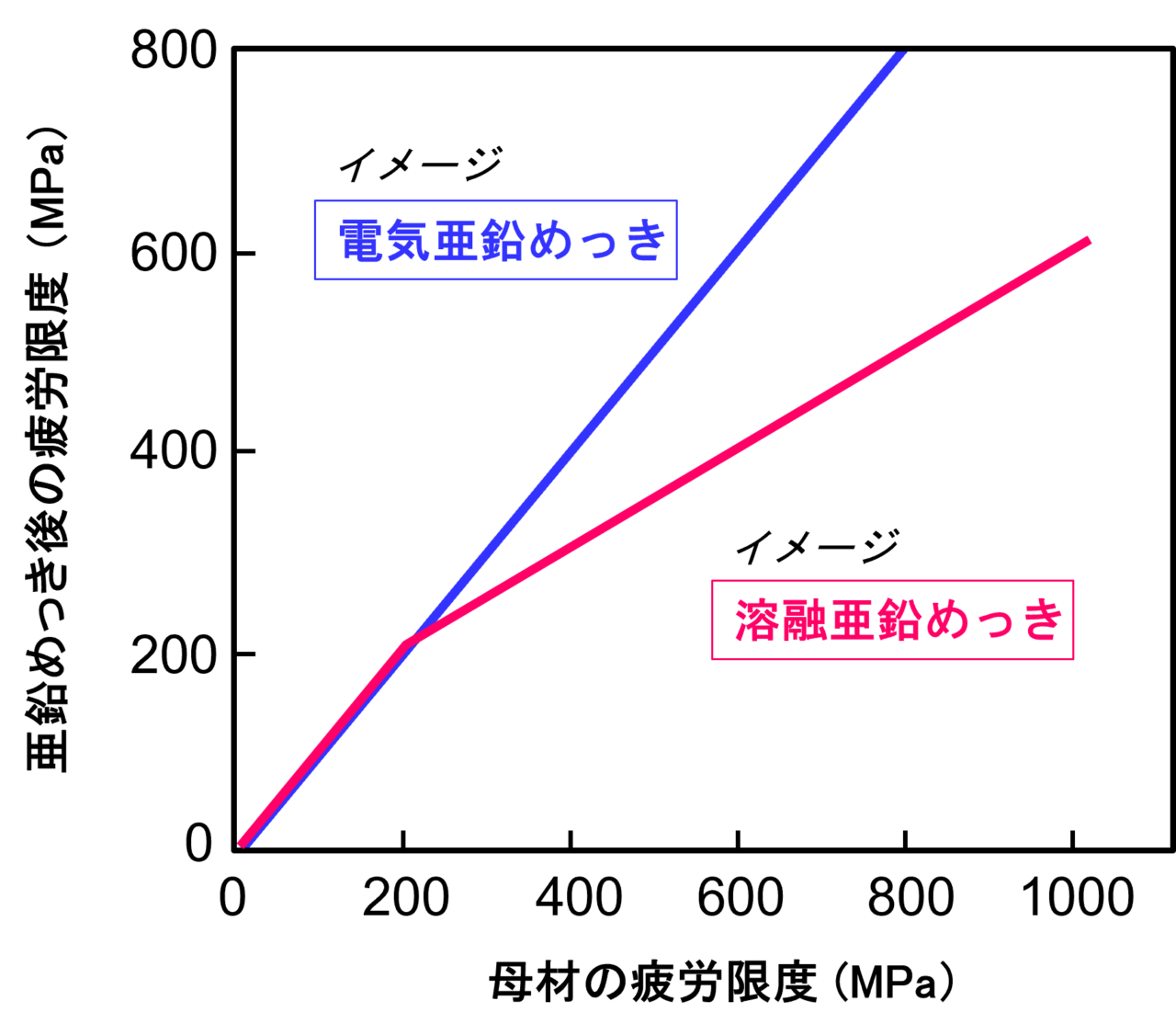
図6.各亜鉛めっきの疲労限度に及ぼす影響(イメージ図)
疲労強度に関連する以下のねじ締結技術ナビ技術資料・コンテンツもあわせてご覧ください。